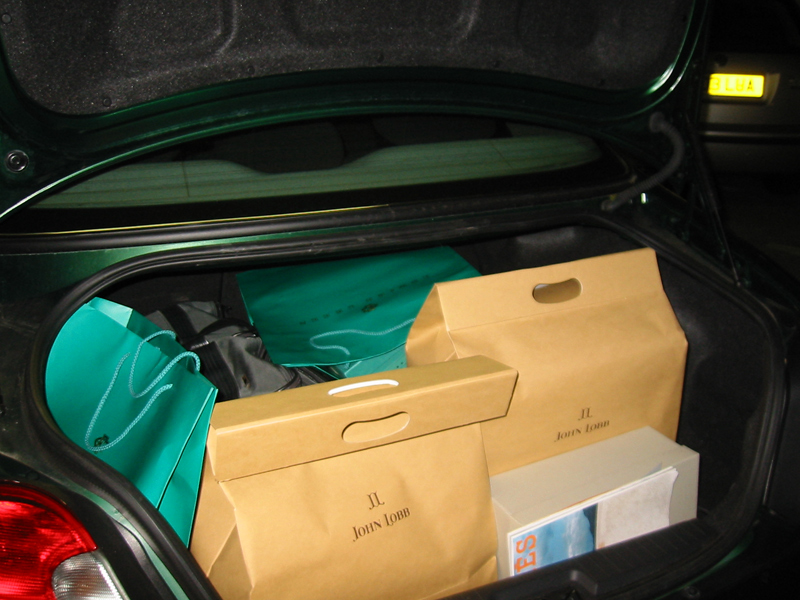
The boot of our car after an afternoon’s shopping in Northampton. Final count – 2 pairs of Edward Greens, 5 pairs of John Lobbs. What a success!
As a detour from a trip I made recently leading a group of watch enthusiasts to the Lange Uhren factory in Glashutte, Germany, I spent the weekend with a Lange's then Joint Managing Director - my good friend Dr. Frank Muller in London. We spent the afternoon in gentlemanly pursuits of browsing the stores in Savile Row, Jermyn Street and at the Burlington Arkade, before spending the evening at Ronnie Scotts with some great Jazz. We hired a car, spent the night in Cambridge University...we stayed in a small hotel right by the campus, and even managed to catch a live choral performance in one of the collages. The next day we went shopping in Northampton oand …ended up with the above spoils.
We called the Edward Green factory ahead, and secured an 11am spot with our hostess – Susie Jones. She met us cheerfully at the door, and showed us around.
The first room we came to, we saw a team of men cutting leather. The process, known as clicking was performed by a highly skilled workman who would cut the individual pieces of leather into patterns. Edward Green shoes use Swiss calf. Bespoke shoes, at that time made under the supervision of Master cordswainer Tony Gaziano, is sent out to outhouses around Northampton. Tony has since left Edward Green and now on his own firm of Gaziano & Girling.
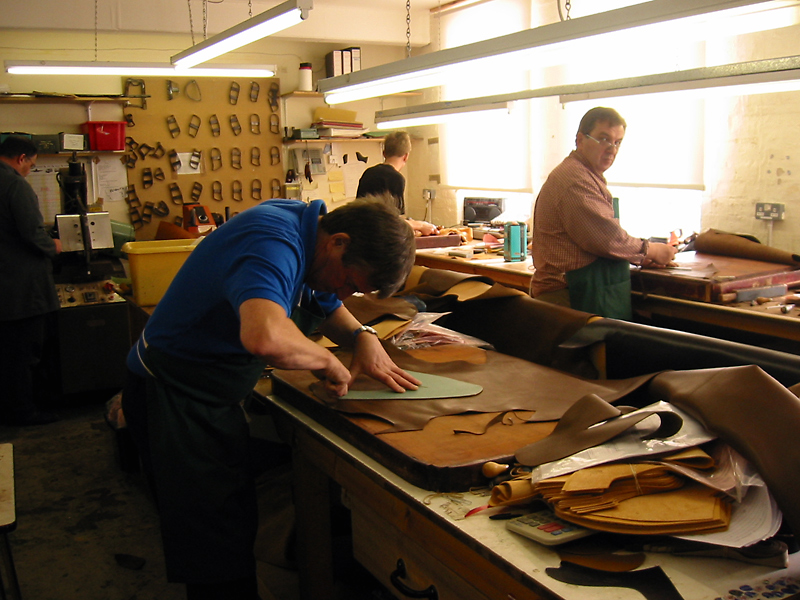
We were told that all clicking for Edward Green was done at this place. The picture below shows a master clicker, placing pieces of leather on his pattern (which, as shown is a piece of green cardboard).
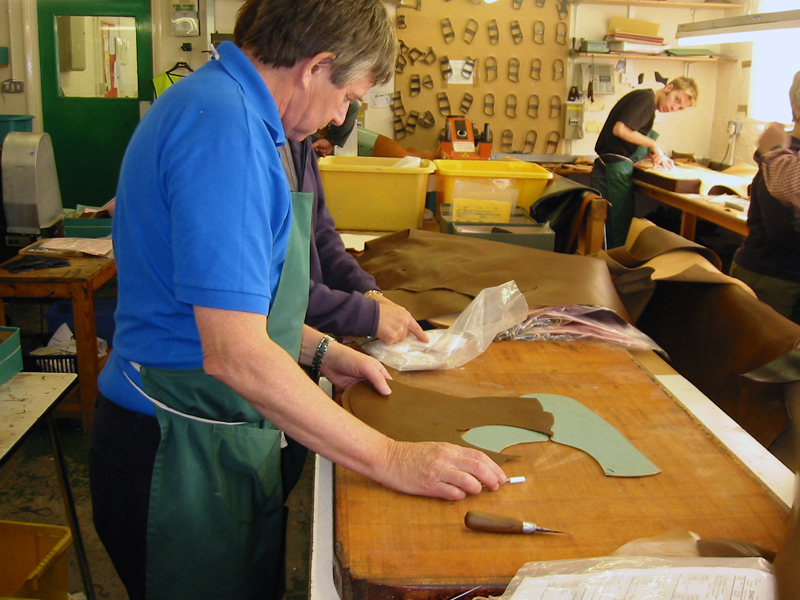
The patterns were then stitched together in these huge sewing machines, like those your mother would use for mending clothes, as shown below.
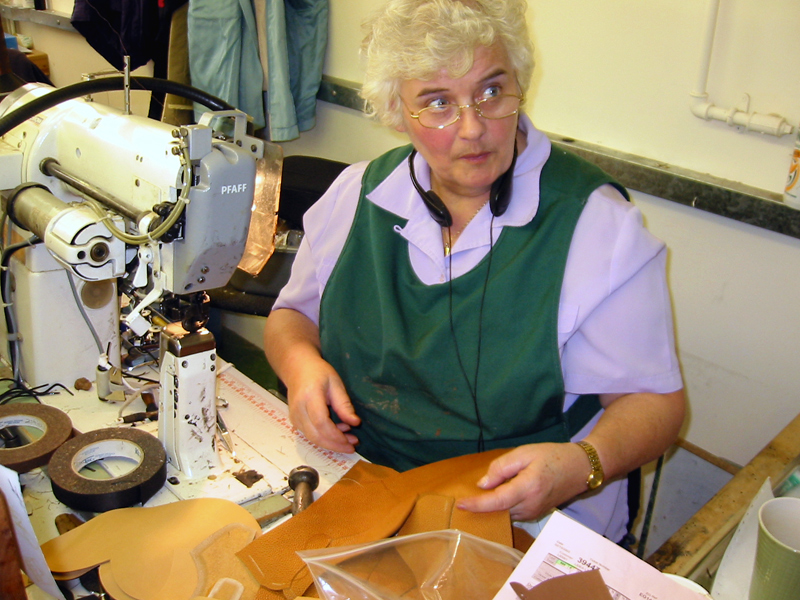
After stitching, the leather takes the shape of an upper.
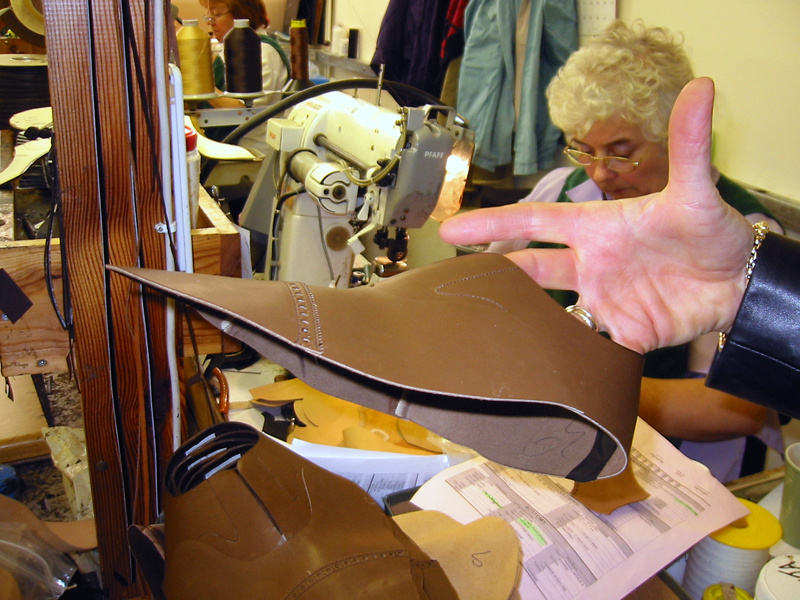
A machine was used to make the perforations in the brogue.
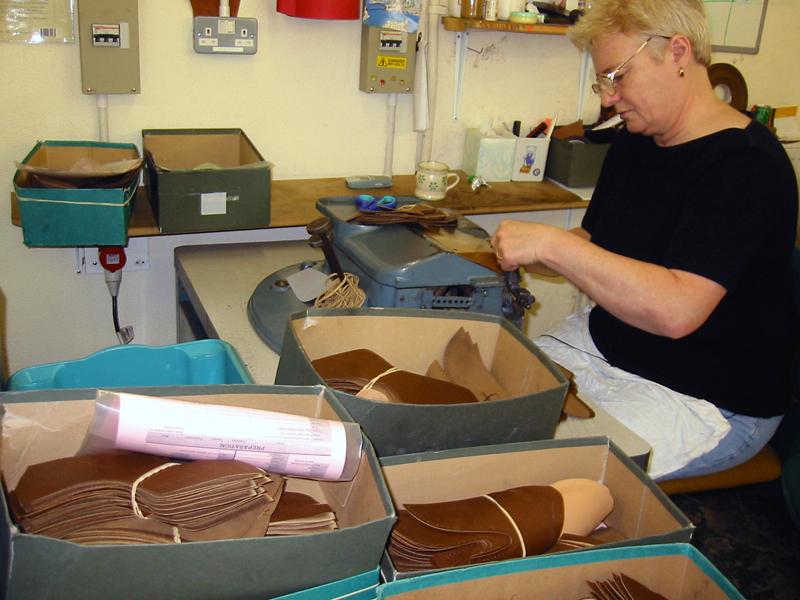
The broging pattern on the upper:
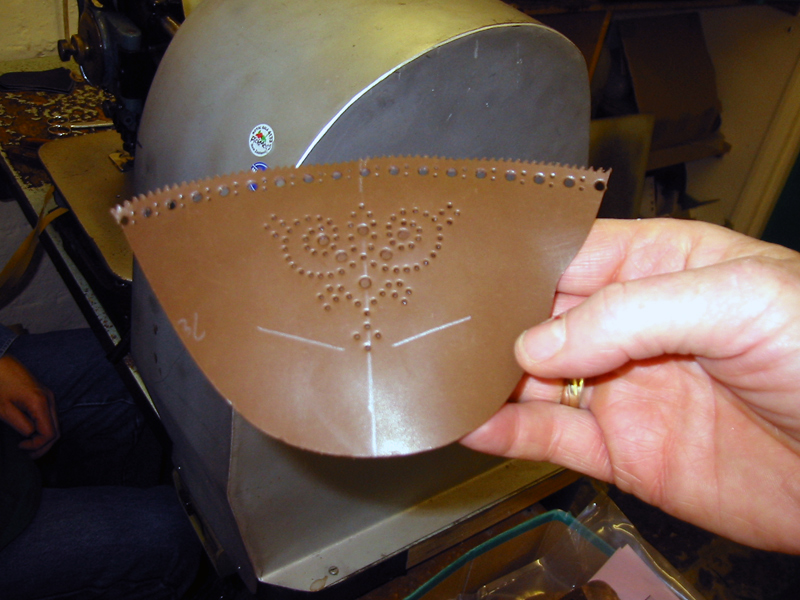
Next, we went to visit the man with the lasts. Here all the lasts were stored. Not sure why I only have the small picture for this shot. Bespoke lasts are kept elsewhere, these are RTW lasts.
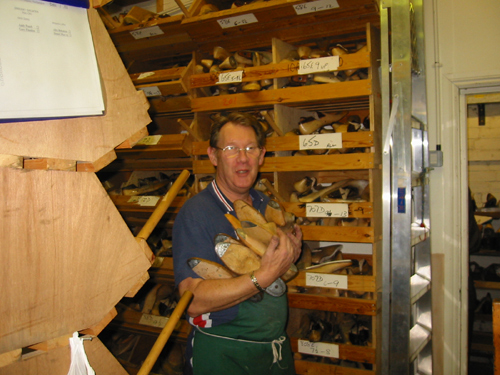
The sewn uppers were then stretched over the last like so. At this stage, the shoelaces were nothing more than pieces of cloth, just to keep the uppers closed.
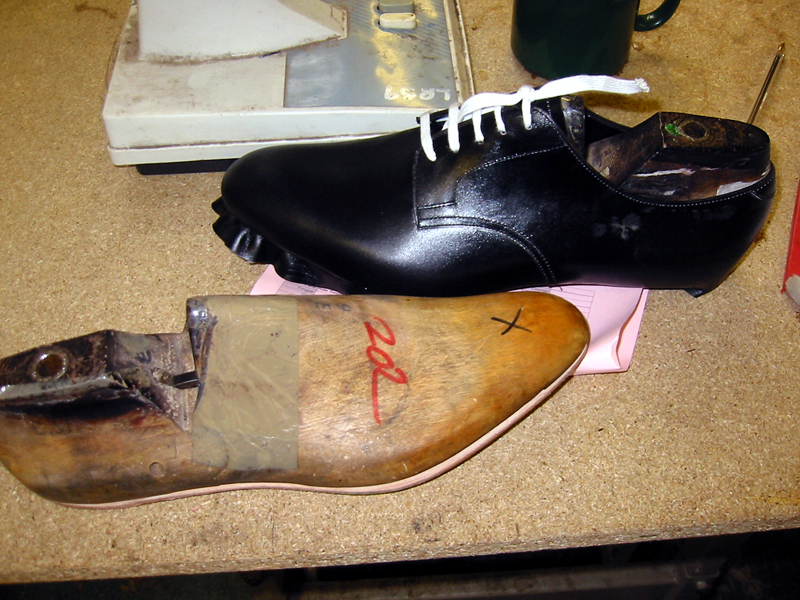
The upper is then nailed onto the last, with temporary nails:
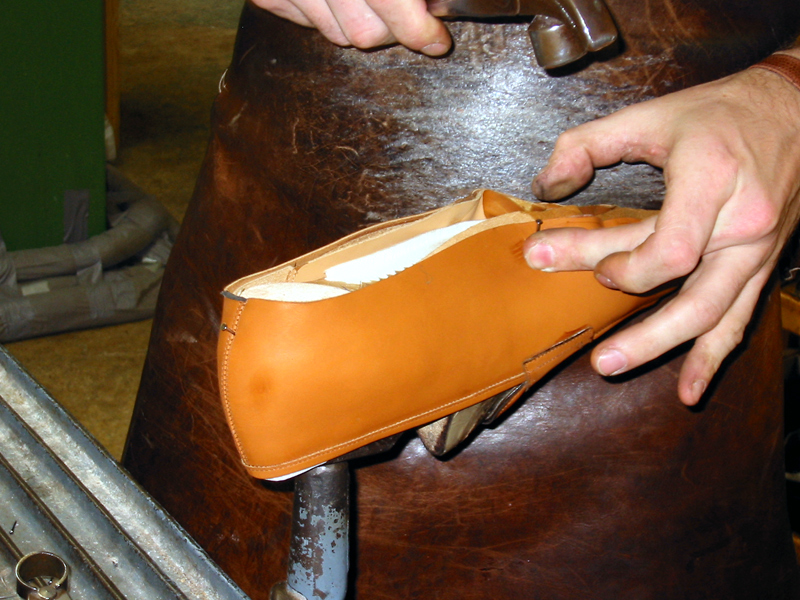
An iron wire is then lopped over the last, and pulled into place, stretching the upper over the last. A machine is used to do this:
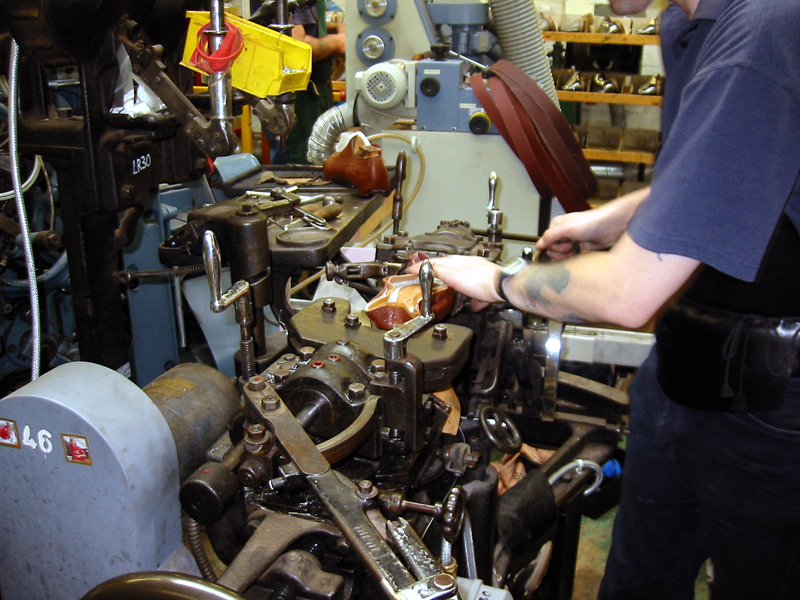
Then, the nails are then removed, and the shoe/last looks like this.
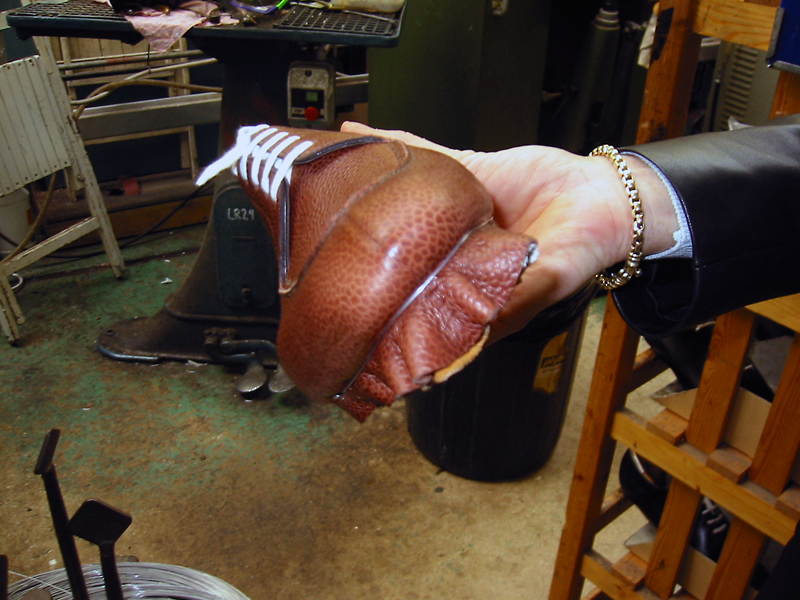
Another team, in the meantime, prepares the soles, but glueing in the feather. In the Northampton tradition, the feather is made from cloth, but the feather of a benchmade shoe can be also made of leather.
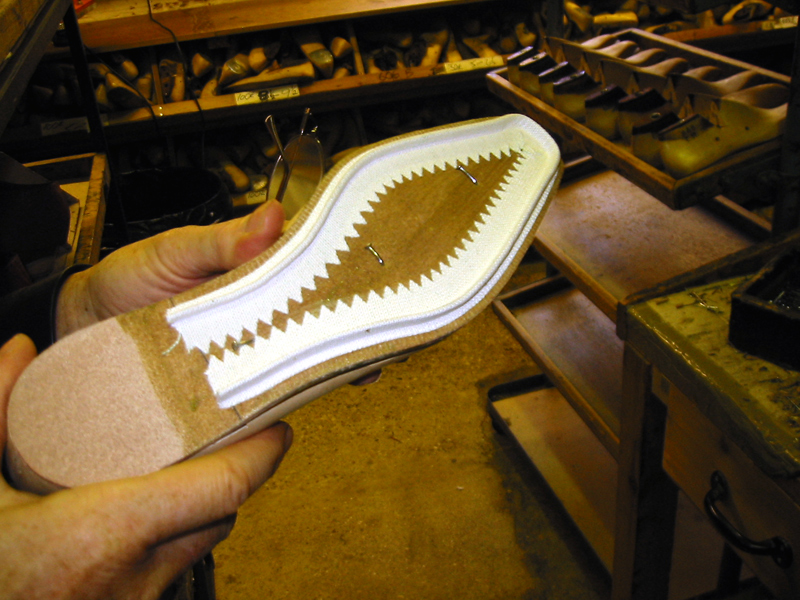
The shoe was then put into a Goodyear welting machine, which did the stiching of the welt, semi-automatically. The operator puts the upper/sole on, clamps it tight, and off the machine goes at a furious pace, finishing the complete welt in less than 20s. EG bespoke shoes are hand stitched, and do not use a Goodyear machine. This process is more involved, and requires more skill from the cordswainer, and of course takes more time.
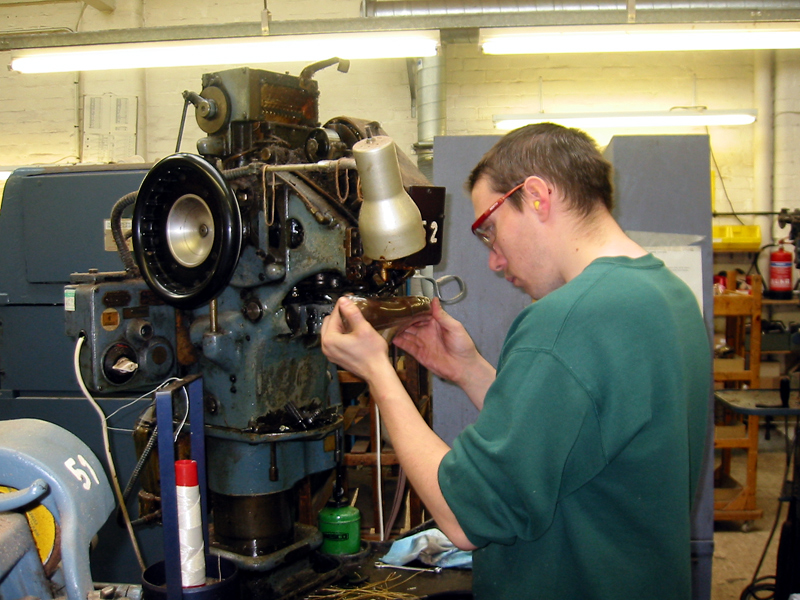
After welting, the inner side is then filled with cork bits:
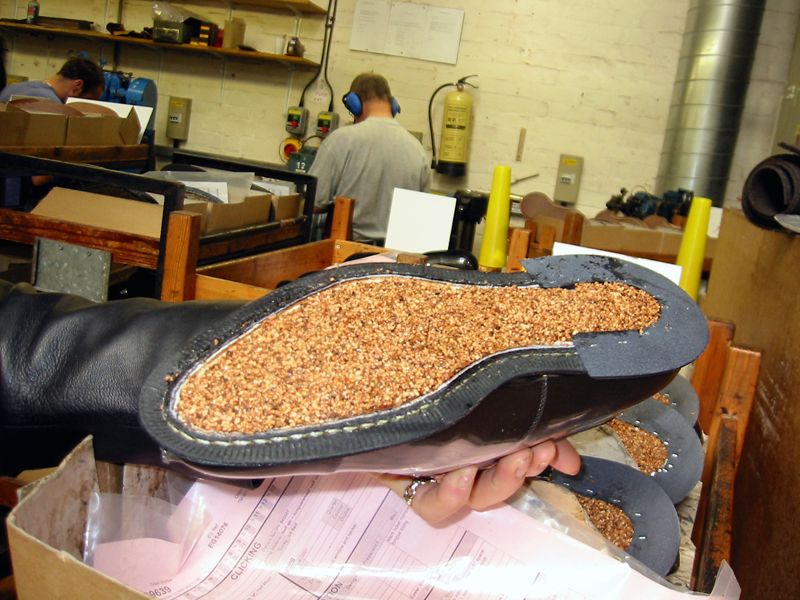
And the shoe is then sent for installing the sole. Backtracking upstairs, we came across these two gentleman, who were in charge of “skin stitching” the aprons and center toe seams. First, the thread is prepared by waxing:
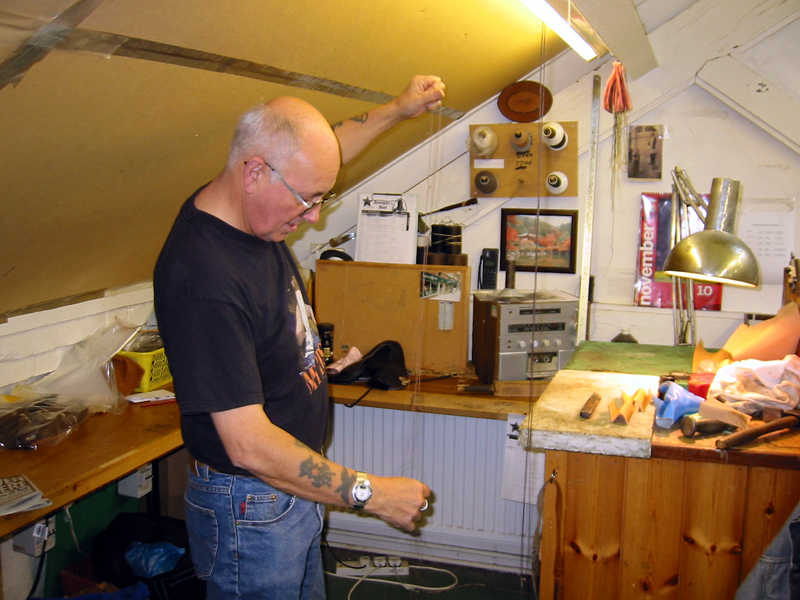
Then, the aprons are stitched using a boar’s bristle. From what I can see, using a boar’s bristle, due to the ability of the bristle to flex, gives a smoother finish on the raised apron than can be achieved with a steel needle. Only Edward Green and John Lobb use this technique of sewing with a boar's bristle.
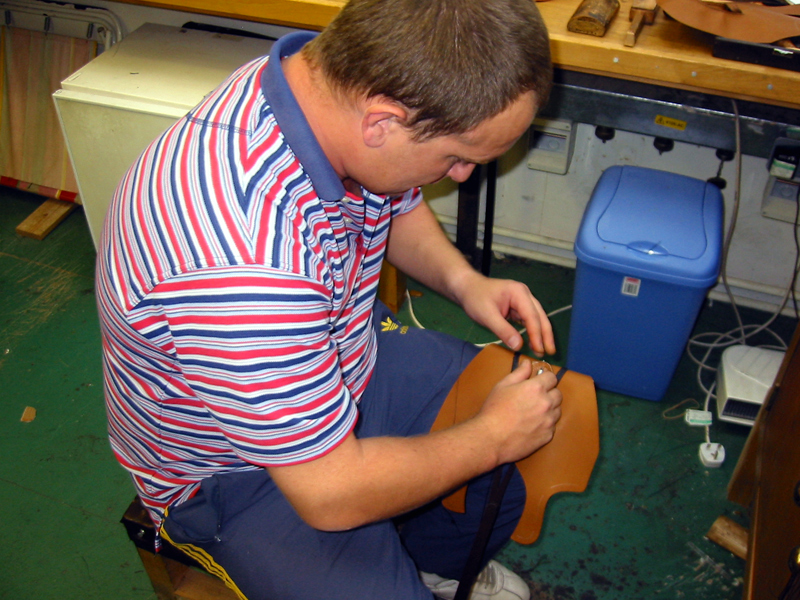
Returning to the shop floor, the outer soles are glued, and stitched on, leaving the thread inside the channels. The shoes then wait with the channels open:
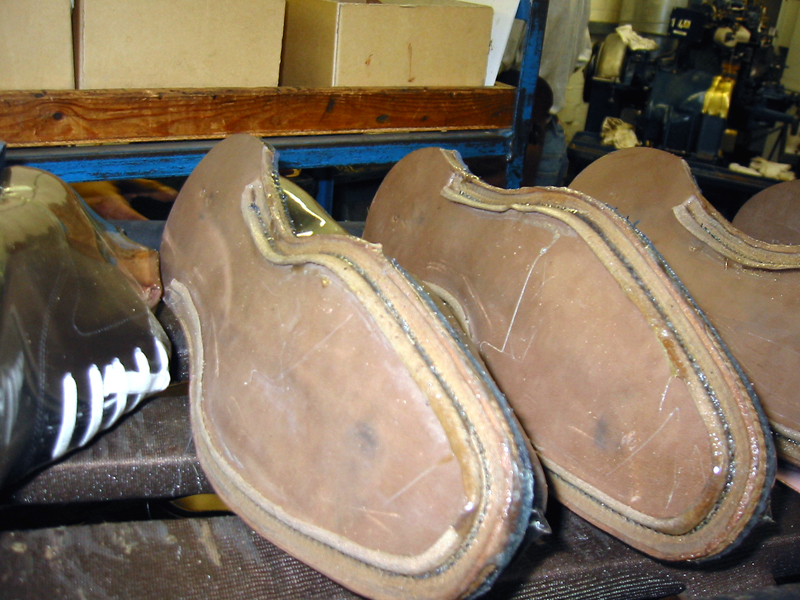
The channel is then closed:
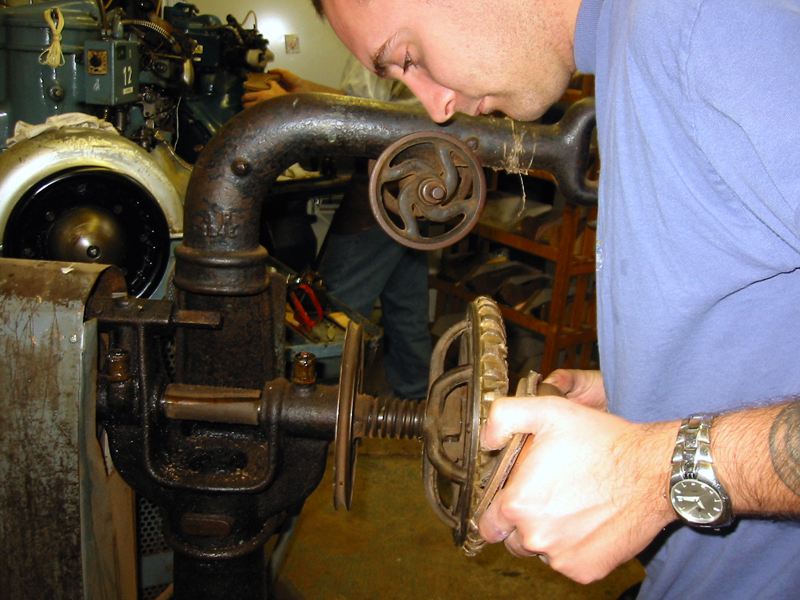
The heels are nailed on:
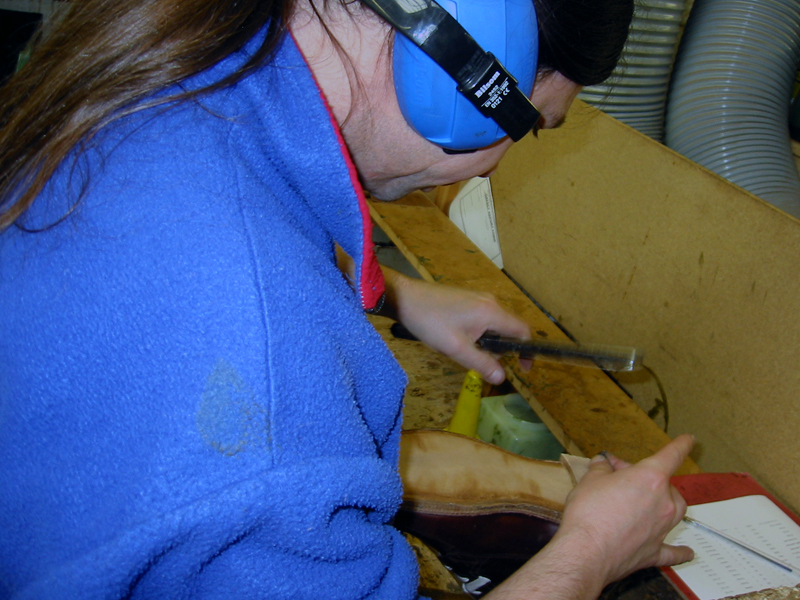
And the final finishing at the factory floor, the soles are cleaned, and a hot iron is used to apply polish to the edges:
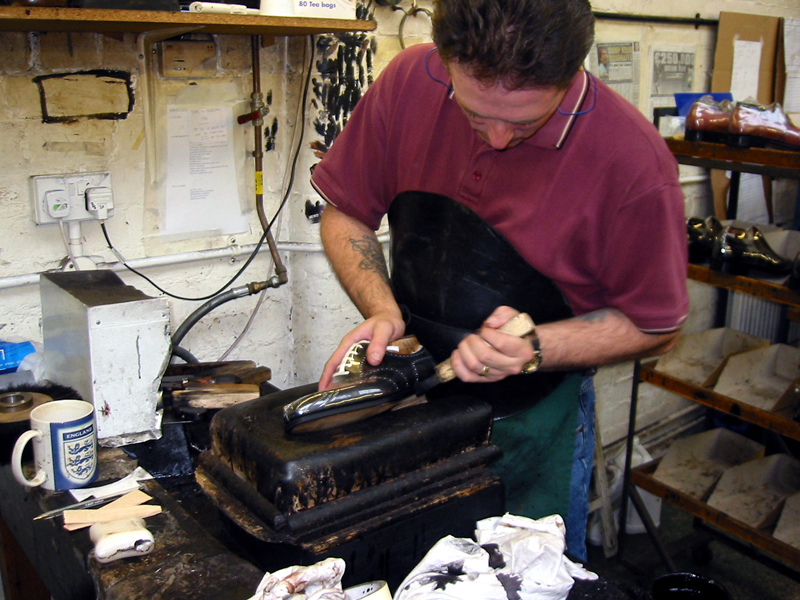
The shoe is then sent to the finishing department, where skilled craftsmen select the final color of the shoe, and finish it to their specifications:
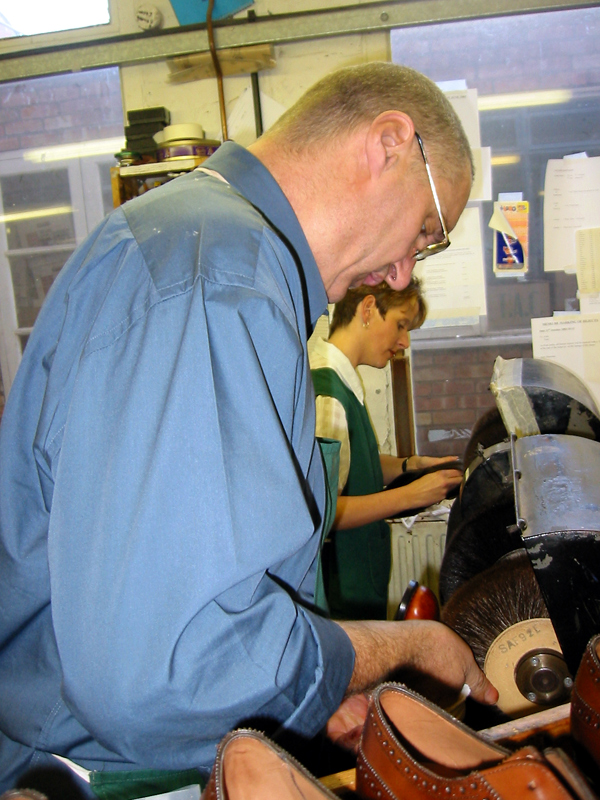
The final product...a beautiful patina, and wonderful shoe. This is the Berkerly in antique oak in the 202 last.
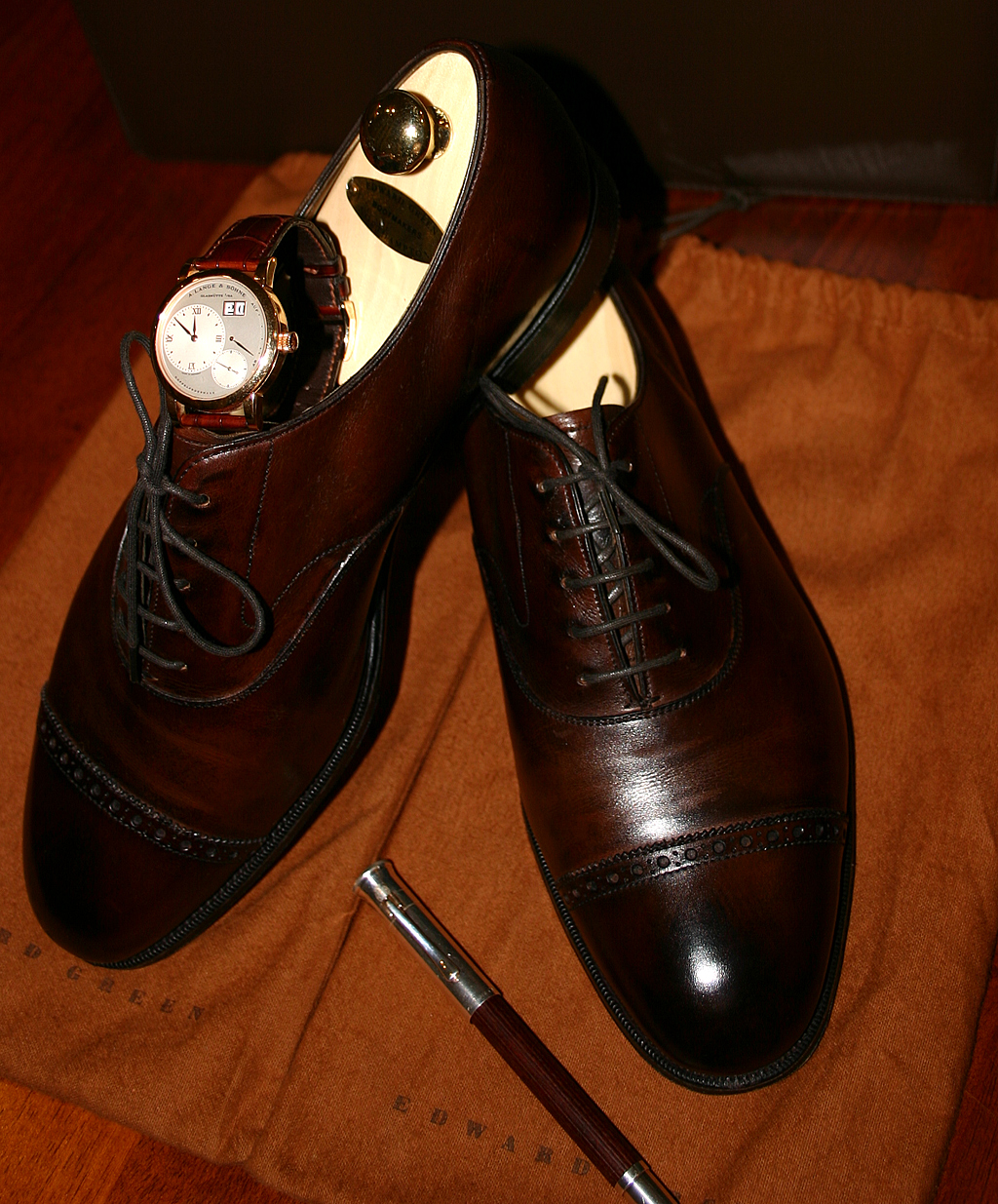